Material Removal
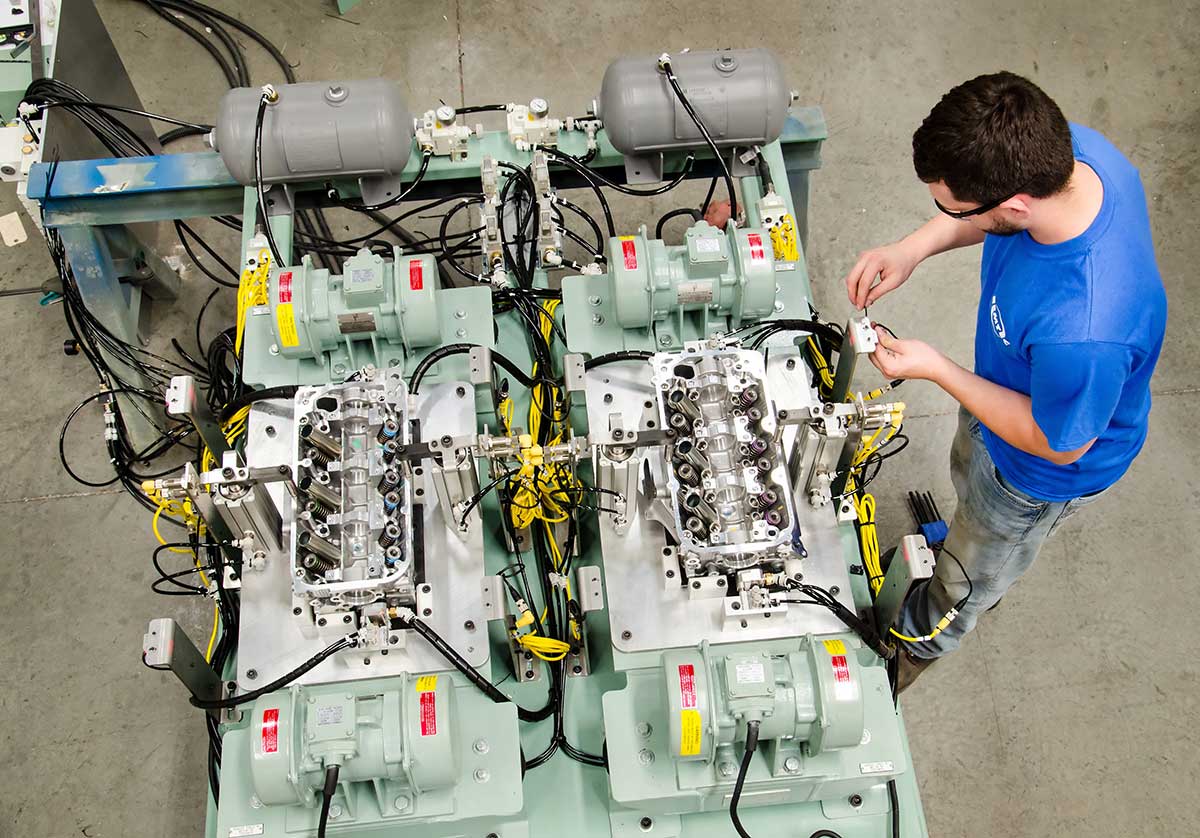
When cast metal parts and plastic molded components are manufactured, it is common for undesired material that has flowed out along parting lines to remain on the piece. This excess material is referred to as flash and needs to be removed to transform a part into a more desirable finished state.
Parts can also have rough edges or ridges, known as burrs, which need to be removed. In some cases, a workpiece may have a surface finish that is not ready for finishing and must be sanded.
How Automation Improves Material Removal Processes
Material removal operations present many inherent challenges. One example lies with wood materials, which can be unstable and change with manufacturing, environmental conditions, species, and more. Problematic from a safety standpoint is the fact that manual removal techniques require operators to handle high speed rotary cutting tools.
Additional problems include:
- Inconsistent levels of quality between operators and shifts
- Overly aggressive material removal which creates scrap
- Hard automation solutions have offered a lack of flexibility
Robotic material removal systems provide a host of benefits to address these challenges. They are scalable, and subsequently lower manufacturing and equipment costs. Robotics can also meet the needs of lower tolerance applications more efficiently than overly precise and costly hard automation. When containment systems are included, sanding dust, chips, etc. can be retrieved, recycled, and controlled for added application advantages.
Operational benefits gained through automated material removal include:
- People no longer have to work in dusty and dangerous environments
- Product quality is increased and scrap is reduced
- Repeatability issues are resolved, throughput is improved, and overall quality is enhanced
Industries that Use Robotics for Material Removal
- Automotive
- Transportation
- Aerospace
- Furniture Manufacturers
- Building Materials
- Plastic & Rubber Component Manufacturers
Why Choose Remtec?
Remtec provides flexible systems that robotically deburr, deflash, cut small chamfers, and sand to finish metal, plastic, and wood pieces. In fact, when all required wood sanding parameters can be reviewed ahead of time, we are often able to develop systems that can progress from rough condition all the way through to a ready-to-apply finish state.
As a supplier, Remtec offers the advantages of:
- Robust system design
- Machine vision based quality check solutions
- Force guided solutions
- Automatic compensation solutions
- Non-standard customizable solutions
- Extensive experience that can be applied to industries and materials
Applying the benefit of our extensive experience, Remtec has been able to develop innovative solutions for a wide range of industries and materials. Our team will identify the most efficient and cost-effective equipment to achieve your process goals while staying within the scope of your budget. We’ll also develop a thorough cost/benefit analysis for your team to see the justification for your robotic automation investment.
In the case of companies that are new to robotics, we’ll work with your team to provide training, easy to use HMI based controls, and anything else necessary to make the integration process easy and accessible.