High-Speed Picking Robots for Packaging Automation
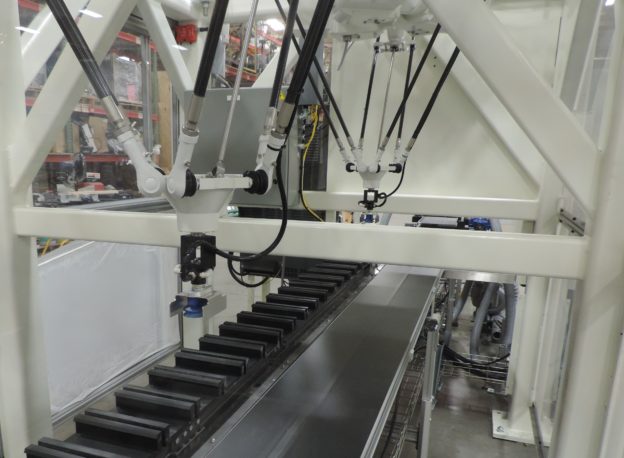
Delta, SCARA, and 6-Axis Solutions for Precise, Vision-Guided Product Handling
What It Is:
Robotic picking systems that use vision guidance to identify, orient, and place products like pouches, tubes, and bottles — even when randomly arranged.
Why It Matters:
Automating picking reduces labor reliance, improves ergonomics, and boosts throughput. Our systems run up to 110 picks per minute and adapt to fast SKU changeovers.
Remtec’s robotic high speed picking systems offer maximum flexibility, with the ability to change SKUs automatically on demand. All of Remtec’s picking robots are equipped with standard Allen-Bradley controllers, which eliminate the need for robot programming expertise on the packaging floor. A simple touch screen operator interface is provided so that the system can be operated without specialized training. Production data is also tracked and displayed.
Picking Robot System Options:
- Product conditioning (pouch flattening, product feeding, and separation)
- Integrated vision inspection
- Product recirculation and/or buffering
- Ethernet integration with a line or plant enterprise systems
Typical Use Cases:
- Loading pouches or tubes into cartons or trays
- Transferring food items into thermoform pockets
- Bottle orientation and placement into retail-ready packaging
- Order fulfillment and sorting for e-commerce
Top Features:
- Vision-guided delta, SCARA, and 6-axis robot options
- Up to 110 picks per minute per robot
- Allen-Bradley PLC-based changeover
- Integration with ERP, conveyors, inspection, and palletizers
- FDA-grade and washdown configurations available
Feature | Specification / Range |
Robot types | Parallel‑link (delta), SCARA, 6‑axis |
Picking rate | Up to 110 pieces per minute per robot |
Vision system | High-speed line tracking, orientation |
Changeover | Automatic SKU change via Allen‑Bradley PLC |
Integration | ERP, MES, conveyors, safety systems |
Common payloads | Pouches, tubes, cartons, bottles, trays |
Case Study: How SS White Automated Tedious Burr Packaging—Without Halting Production
When labor shortages and ergonomic risks slowed a top dental burr manufacturer, Remtec delivered a flexible robotic solution that transformed output, safety, and operator efficiency.
- One operator now runs 6+ production cells
- Automatic SKU changeovers with no downtime
- Zero programming required — touchscreen control
Frequently Asked Questions
Picking robots use high-speed vision systems to locate items—often randomly oriented—on moving conveyors. The system calculates their position and orientation in real time, enabling the robot to pick and place each item precisely into a tray, pocket, or carton.
Remtec’s systems are used across rigid, flexible, and semi-rigid formats. Common examples include pouches, tubes, bottles, blister packs, thermoformed trays, and cartons.
Each robot can pick up to 110 items per minute depending on product size, weight, and orientation. Systems can be scaled by adding multiple robot units.
Industries include:
- Food & beverage (pouch loading, case/tray packing)
- Pharmaceuticals (tube or blister pack handling)
- Consumer goods (multi-pack arrangements)
- E-commerce (automated order picking)
Picking robots are typically integrated with:
- Upstream conveyors or infeeds
- Downstream tray formers, cartoners, or case packers
- Vision inspection systems
- Safety enclosures and guarding
- Plant control systems (via Ethernet/IP, OPC UA, etc.)